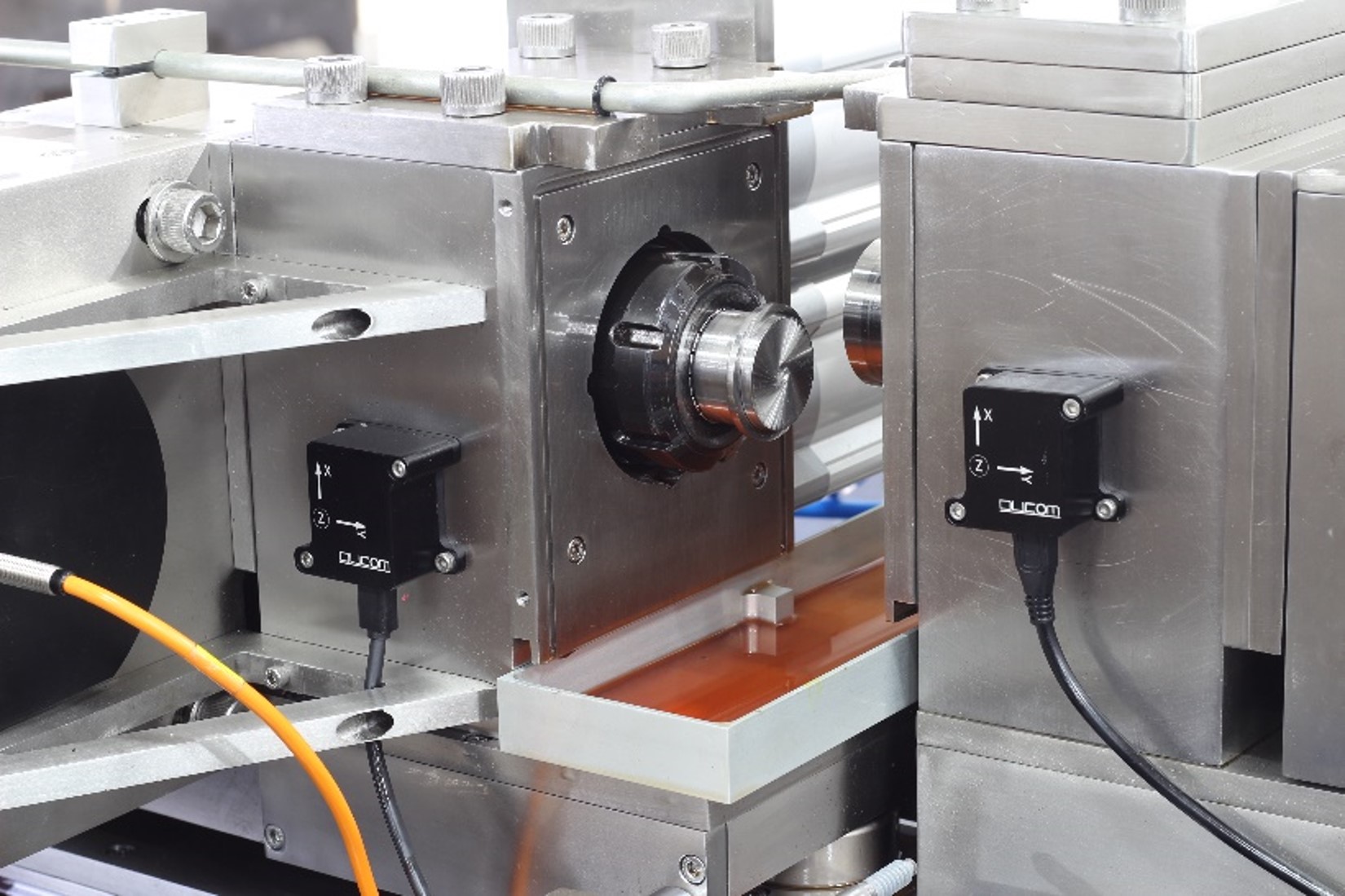
traction machine for lubricants
Precision measurement of Stribeck curve, traction coefficient, scuffing & lubricated fatigue wear OF LUBRICANTS ON A SINGLE PLATFORM
Beyond Mini Traction Machine
Ducom Twin Disk compared to Mini Traction Machine has the following advantages (Table 1):
- Twin Disk offers > 3 GPa contact pressures and realistic elliptical contacts using steel-steel pairs as compared to traction machine which can achieve it only by using either tungsten carbide (WC) materials or edge loaded barrel geometries. One can carve rollers from field components (Ex. Rails/Wheels) and be used in twin disk.
- Twin Disk can reproduce and exceed the FZG load steps, so it can be considered as a precursor to FZG.
- Twin Disk with in situ friction, vibration and eddy current sensor is used for Friction, Fatigue and Wear Tests.
- Twin Disk with electric contact resistance (ECR) can be used to determine the distribution of lubricating film at the contact without compromising on realistic tribopair (i.e., transparent disk in MTM to measure film thickness).
The Ducom Twin Disk Tribometer is used for friction, fatigue and wear testing of materials that experience rolling and sliding, like materials used in rolling element bearings, gears and cam followers within the transportation industry. Rolling sliding contacts are integral to bearings, power transmission systems, rail-wheel interface, rolling mills that are typically subjected to high contact pressures (1.5 to 4 GPa) and slip ratios (0 to 100%). Traction, Stribeck and scuffing characteristics of lubricants, governed by the base oil and additive chemistry is used to improve the efficiency and durability of these machine elements.
Traction test
The load was kept constant at a line contact (1 to 2 GPa contact pressure) and the % slip varied between 0 and 50%. A peak in the coefficient of friction was observed with lower % slip indicating the limiting shear stress under elastohydrodynamic (EHD) conditions. The lubricant temperature also increased at higher % slip indicating thermal effects due to EHD shearing.
STRIBECK CURVE FOR LUBES
Stribeck tests were conducted with decreasing entrainment velocity (0.001 to 10 m/s) at constant line contact pressure (4 GPa). A transition from EHD to boundary lubrication was observed with the friction coefficient increasing from 0.05 to 0.15 representative of non-conformal contacts.
SCUFFING TEST
During scuffing tests, two different motions were used (a) co-rotation with a finite lubricant entrainment velocity (b) counter-rotation with near zero lubricant entrainment velocity. The load was increased in steps till either a sharp increase in friction (COF > 0.2) and/or vibration were observed. Under co-rotation the coefficient of friction was constant up to loads of 5kN (~2.3 GPa peak contact pressure). With counter-rotation however, there was simultaneous increase in friction coefficient and vibration at ~ 3 kN (1.8 GP contact pressure) indicating scuffing. Microscopy of the disc surfaces post-test indicated severe material transfer and surface damage.
Such test methods using twin disc can effectively and quickly screen different base oil and additive chemistries in a repeatable manner and enable development of lubricants for electric vehicles and high-speed railways.